Prestar atención al mantenimiento del sistema eléctrico evitará que te quedes varado tras apagar el camión para descansar; especialmente ahora que los camiones tienen cada vez más componentes que funcionan con electricidad. También es crucial para no tener pérdidas repentinas de potencia y alargar la vida útil del alternador.
El alternador es el componente de tu camión que conecta el motor y el sistema eléctrico. Convierte la potencia de rotación del cigüeñal en corriente de 14 voltios para cargar las baterías y operar todas las luces, los indicadores, el ECM del motor y la parte electrónica del sistema de inyección. El motor de arranque desempeña el papel inverso: convierte la electricidad almacenada en la batería en energía de arranque.
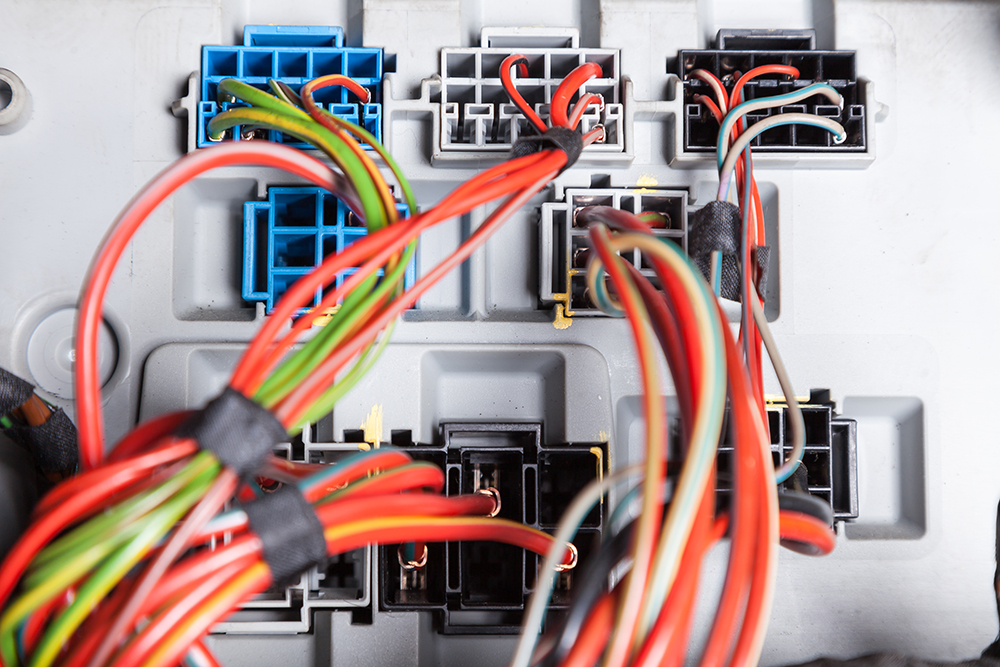
Si bien el alternador prácticamente no presenta problemas, su funcionamiento y su larga vida útil dependen del mantenimiento de la batería y de todo el cableado y los sistemas de tierra que garantizan circuitos eléctricos de baja resistencia. Un determinado síntoma del sistema eléctrico puede indicar un problema en una o más áreas, por lo que el mantenimiento y la resolución de problemas no deben limitarse a uno o dos componentes.
Mantenimiento de la batería
El mantenimiento del alternador se trata más de mantener las baterías que del alternador en sí. Un buen alternador dura casi para siempre, pero sólo si no se sobrecalienta. Una buena forma de evitar dicho sobrecalentamiento es mantener las baterías funcionando de manera eficiente.
La función principal del alternador es manejar la carga eléctrica del vehículo, consumiendo el 75 por ciento o más de su potencia. Las baterías nuevas y un buen cableado reducen las necesidades de carga de la batería, lo que facilita la vida del alternador. A medida que las baterías y los cables desarrollan resistencia, el alternador trabaja más y durante más tiempo para reemplazar lo que se usa para arrancar o suministrar cargas de apagado nocturno.

Es fundamental probar las baterías una vez al año, preferiblemente justo antes de que empiece a hacer frío.
Prueba de potencia de arranque confiable
1. Desconecta los cables para aislar las baterías.
2. Utiliza un probador de carga de pilotes de carbono (una gran resistencia eléctrica) para aplicar la mitad de la carga nominal a cada uno.
3. Verifica el voltaje de salida durante 20 segundos de carga continua con un voltímetro. Si el voltaje se mantiene en 9.5 voltios o más durante más de 20 segundos, la batería está en condiciones de arrancar el camión.
El voltaje de una batería que está a punto de fallar disminuirá al cabo de 20 segundos. Si alguna batería no supera esta prueba, reemplaza todo el conjunto para garantizar una larga vida útil. Puedes realizar esta prueba de forma económica en un distribuidor o taller de reparación si no puedes hacerlo tú mismo.
Si bien esta prueba ayudará a garantizar arranques confiables, es más difícil determinar si las baterías están comenzando gradualmente a sobrecargar el alternador al perder su capacidad de reserva, señala Bruce Purkey, presidente de Fleet Electric de Purkey. Sugiere dos formas de comprobar esto:

Capacidad de reserva de prueba
1. Establece una base para obtener baterías en buen estado probándolas cuando sean nuevas.
• Apaga el motor. Mide el voltaje de la batería.
• Enciende las luces y déjalas agotar las baterías durante 30 minutos. Vuelve a probar el voltaje de salida y registra la lectura.
• Después de uno o dos años, puedes repetir la prueba. Después de 30 minutos, si el voltaje cae más que cuando estaba nuevo, muestra una reducción en la capacidad de reserva.
2 Supervisa cuidadosamente el rendimiento de la batería mientras está apagada durante la noche si tienes un inversor con corte de bajo voltaje. Si su carga nocturna típica es bastante constante, ten en cuenta cuánto tiempo lleva recibir una advertencia o un corte de bajo voltaje. Cuando ese intervalo se acorta significativamente, es hora de reemplazar las baterías.
Las baterías convencionales requieren la adición regular de agua destilada. Mantén las celdas llenas para obtener el máximo rendimiento y vida útil, haciéndolo una vez al mes. Cuando realices tu control mensual del nivel de electrolitos, limpia con cuidado la parte superior de cada batería. Haz esto también con las baterías sin mantenimiento. Mantener las baterías limpias reduce la pérdida de carga durante las paradas.
Las baterías convencionales tienen la ventaja de que la densidad del electrolito líquido en las celdas se puede comprobar fácilmente con un hidrómetro. Retira la tapa de cada celda, extrae una muestra de electrolito en el hidrómetro y observa lo que hacen las bolas indicadoras. Si suben a la superficie del líquido, la celda está cargada. Si se hunden, la celda está defectuosa y se debe reemplazar la batería. Siempre devuelve el electrolito a la celda una vez probado. Realizar pruebas cada seis meses es una excelente manera de anticipar problemas con la batería.
Las baterías libres de mantenimiento tienen un indicador que cambia de color cuando se deterioran. Consulta el manual del propietario para obtener una descripción de cómo debe verse el indicador. Cuando cambie de color, haz revisar la batería y, si es necesario, reemplázala.
Más consejos sobre MP de batería
• Limpiar y apretar las conexiones. Dos veces al año desconecta todos los conectores de la batería y utiliza un cepillo motorizado para limpiar tanto el diámetro interior de cada conector como el poste. Vuelve a conectar todas las conexiones de forma segura y luego cúbrelas con grasa dieléctrica o un protector en aerosol. Ten en cuenta que los conectores de cables blandos típicos se estiran continuamente. Aprieta los pernos de sujeción una vez al mes para garantizar la máxima conductividad, u obtener conectores de latón chapado que son mucho más duros.
• Ten cuidado con las temperaturas frías. El clima frío afecta la capacidad de una batería para liberar la energía almacenada y permitir la recarga. “Una batería perderá el 35 por ciento de su amperaje de arranque en frío a 0 grados Fahrenheit”, dice Purkey, “por lo que necesitas una carga completa de la batería para garantizar un arranque confiable. También tenga en cuenta que un arranque rápido puede no ser suficiente para preparar el camión para una parada, incluso unas horas más tarde. A temperaturas frías, las baterías pueden tardar hasta dos días en cargarse completamente”.
Esto significa que conectar el camión a un cargador de batería es la mejor manera de hacer que el camión vuelva a funcionar de manera confiable, dice Tim Ruth de Warehouse Battery Outlet. “Para llevar una batería descargada a su carga completa de 12.6 voltios, cárgala a baja velocidad durante 18 a 24 horas, no sólo 2 o 3 horas”, comentó.
Mantenimiento del cableado
Purkey dice que muchos cables de batería han sido los verdaderos culpables cuando los propietarios de camiones creen que tienen un problema de carga o de batería. Entonces, cuando revises tus baterías antes del clima frío, inspecciona también los cables. La práctica recomendada 129 del Consejo de Tecnología y Mantenimiento exige una caída de voltaje de 0.5 voltios o menos a 500 amperios de flujo de corriente. Si la caída de voltaje es mayor que esto, es necesario reemplazar el cable.
Sin embargo, no se puede saber mucho simplemente colocando un voltímetro en las conexiones porque la resistencia no aparece hasta que hay alta corriente. Por eso, Purkey recomienda que un profesional pruebe cada cable con un instrumento especial que utiliza electrónica para medir la resistencia. En cuatro segundos, un técnico puede saber si es necesario reemplazar un cable.
Alternadores y calor
A medida que el cableado dentro del alternador se calienta, la resistencia aumenta, lo que reduce la salida de la unidad. Los devanados interiores tienen aislamiento y conexiones soldadas sensibles al calor. A medida que las cargas aumentan más allá de lo que fue diseñada la unidad, esta puede fallar. Una carga inusual puede tener el mismo efecto que las baterías ineficientes, produciendo un efecto de bola de nieve que significa largas horas con cargas máximas, sobrecargando el alternador.
También puedes hacerlo tú mismo. Mide el voltaje en el conector positivo del motor de arranque mientras otra persona arranca el motor. Luego toma una medida similar en el terminal positivo de la batería y resta la primera lectura de la segunda. “Tiene mucho más sentido reemplazar un cable de batería de $4 que una batería de $80 cuando el problema es en realidad el cable”, dice Purkey. Él recomienda revisar el cableado trimestralmente o cada vez que vea que comienza a desarrollarse corrosión. “Si puedes ver verde, hay más corrosión que aún es invisible”, comenta.
Más consejos de cableado
• Es necesario verificar las conexiones positivas y de tierra del motor de arranque y del alternador y cualquier cable de tierra en el chasis para garantizar que las conexiones estén limpias y apretadas. Inspecciona y, según sea necesario, limpia las conexiones de cableado, ya sea de voltaje o de tierra. Puedes limpiar las superficies de contacto con un abrasivo como papel de lija. Luego vuelve a instalar los sujetadores firmemente y reemplázalos si están corroídos.
• Inspecciona todo el cableado en busca de aislamiento agrietado o deshilachado o roce contra otras piezas. Repara el cableado defectuoso y protégelo usando bridas para mantenerlo alejado de las superficies circundantes.
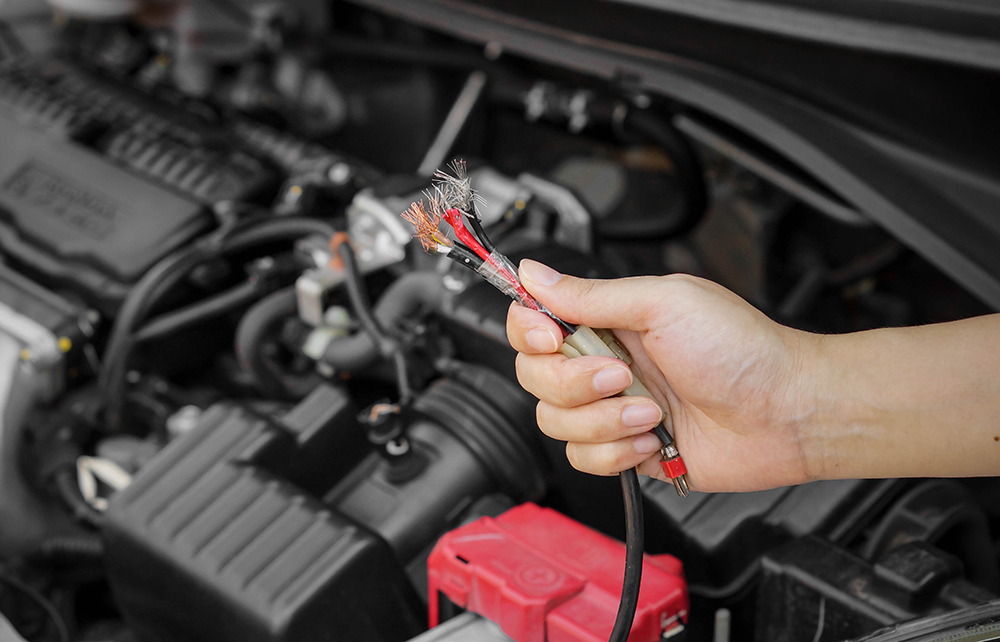
Mantenimiento del sistema de refrigeración del alternador y de la banda
Tu alternador tiene un sistema de enfriamiento: un ventilador que fuerza el aire a través de pasajes en los devanados. Este flujo de aire mantiene la resistencia lo suficientemente baja para un buen rendimiento y protege el aislamiento perecedero y las conexiones internas a menos que se vean amenazados por aspas de ventilador sucias o conductos obstruidos, dice Purkey. El problema con la ubicación del alternador es que son comunes las pequeñas fugas de aceite en el compartimiento del motor. El polvo se adhiere a la capa de aceite y eventualmente cubre las aspas del ventilador y posiblemente obstruye los conductos de enfriamiento. Si ves aceite en el alternador, rastréalo hasta la fuente y repara la fuga. Luego, limpia cuidadosamente las aspas del ventilador y las entradas de aire en el cuerpo del alternador con un trapo limpio para restaurar el flujo de aire.
Dado que el diésel es la principal fuente de energía del camión, es importante mantener el sistema de correas que hace girar el alternador en óptimas condiciones. Dado que las correas dependen de la tensión para la fricción que las hace efectivas, verifique el mecanismo tensor y el sistema de montaje del alternador.
Comprobando la banda y sistema de montaje
1. Coloca una llave en cada perno de montaje del alternador y en cualquier perno ajustable que permita ajustar la tensión de la correa para asegurarse de que todos los pernos estén ajustados. Además, observa la alineación de las poleas para asegurarte de que el alternador y las ranuras de la polea tensora o del cigüeñal estén rectas una frente a la otra. Si la parte posterior de la correa se dobla hacia los lados en cualquier dirección al salir de la ranura de la polea, el accesorio en sí o alguna otra parte del sistema está suelto o tiene un soporte doblado o uno de diseño incorrecto. Es necesario reemplazar los soportes deformados o incorrectos, al igual que los pernos faltantes.
2. Inspecciona cada banda, buscando grietas en la banda exterior o en el interior donde la banda pasa por la ranura. Mira cuidadosamente la superficie de fricción a cada lado del área en forma de V. Si hay algún signo de grietas, o si estas dos superficies están lisas por el deslizamiento, lo que se conoce como “vidriado”, se debe reemplazar la banda. Cuando se utilizan bandas serpentinas que rodean varios accesorios, verifica que no haya los mismos tipos de grietas y vidriados, además de deshilachados que comiencen en los bordes exteriores y avancen hacia el centro. Además, revisa que la correa esté limpia y seca. Si está empapada de aceite, reemplázala y repara la fuga de aceite. Cambia las poleas que sean tan viejas que tengan ranuras donde pasan las bandas.
3. Prueba la tensión de todas las bandas que se pueden ajustar manualmente con un medidor de tensión. Puedes buscar la tensión requerida en el manual del propietario. Los técnicos experimentados en bricolaje pueden probar la tensión con el pulgar. Debería poder presionar la correa entre media pulgada y tres cuartos de pulgada por cada espacio de 10 pulgadas entre las poleas. El cinturón debe estar ajustado, pero ligeramente elástico, no sólido como una roca. Ajusta la tensión si es necesario aflojando los pernos de montaje y ajuste, girando el accesorio con un dado para obtener la tensión correcta y luego volviendo a apretar los pernos.
4. Si los accesorios son accionados por banda serpentina, el sistema tendrá un tensor automático. Verifica para asegurarte de que la línea indicadora del tensor se encuentra entre las dos líneas cercanas al bloque. Si el indicador está fuera de las otras dos líneas, entonces el tensor está débil o se ha instalado una banda de tamaño incorrecto. Cualquiera de las dos condiciones hace imposible que el tensor haga su trabajo. Si hay algo de tensión en la banda pero el indicador no está donde debería estar, reemplaza la banda con una de la longitud correcta.
5. Para comprobar el tensor, aléjalo de la banda con un desarmador hexagonal para eliminar la tensión y luego desconecte la banda. Ahora usa el desarmador para girar lentamente el tensor desde su posición neutral completamente hacia adentro. Si sientes aspereza o fricción excesiva, el amortiguador del tensor está desgastado y se debe reemplazar la unidad. Reemplace la banda y arranca el motor. Si el tensor funciona correctamente, la correa funcionará sin problemas. Si la correa vibra y el tensor no permanece en una posición relativamente estable, esta es otra señal de que el amortiguador del tensor está desgastado y debe reemplazarse.